История
История сварочных электродов тесно связана с развитием сварки и сварочных технологий. В 1802 году профессор В.В. Петров использовал электроды в экспериментах для исследования свойств электрической дуги. В 1882 году русский изобретатель Николай Николаевич Бенардос предложил применять электрическую дугу для соединения металлических кромок. Почти одновременно с ним начал работу Николай Гавриилович Славянов, который внес усовершенствования в изобретение Бенардоса. Славянов заменил угольный электрод на металлический плавящийся стержень схожего химического состава со свариваемым металлом. Он также использовал расплавленный флюс для защиты сварочной ванны от окисления и выгорания металла, а также для предотвращения накопления вредных примесей серы и фосфора в сварном соединении.
В 1904 году шведский изобретатель Оскар Кьельберг основал фирму "ESAB", которая занималась применением сварки в судостроении. Кьельберг разработал технологию с использованием покрытых плавящихся электродов. Покрытие стабилизировало горение электрической дуги и защищало зону сварки. В 1906 году был получен патент на эту технологию. Использование покрытых плавящихся электродов стало основой для развития и применения сварочных технологий в различных отраслях производства.
В 1911 году англичанин А. Строменгер улучшил электродное покрытие. Он предложил использовать асбестовый шнур, пропитанный силикатом натрия, и наматывать его на металлический стержень. Это защищало сварочную ванну и металл сварного шва от атмосферного воздуха путем образования шлака. Алюминий служил раскислителем и удалял кислород. Эти электроды получили название "Квази-арк" и были широко распространены в Европе и Америке.
В 1914 году С. Джонсу выдали британский патент на метод получения электрода с покрытием, которое наносилось методом опрессовки. Металлический стержень проталкивался через фильеру одновременно с шихтой, ложившейся на стержень.
В 1917 году американские ученые О. Андрус и Д. Стреса разработали новый тип — стержень, обёрнутый бумагой, которая пропитана силикатом натрия. Это покрытие выделяло дым в процессе сварки, защищая сварочную ванну от воздействия воздуха. Бумага обеспечивала моментальное зажигание электрической дуги и стабилизацию ее горения. В 1925 году англичанин А. О. Смит улучшил электродное покрытие с использованием порошкообразных защитных и легирующих компонентов. Французские изобретатели О. Са-разен и О. Монейрон также разработали покрытие, включающее соединения щелочных и щелочноземельных металлов.
Таким образом, в первой четверти XX века были разработаны:
— конструкции плавящихся электродов для ручной дуговой сварки
— методы их изготовления
— обоснован состав покрытия.
Электродные покрытия содержали специальные компоненты: газообразующие, легирующие, шлакообразующие и стабилизирующие вещества. В дальнейшем разработки сконцентрировали на компонентах, входящих в состав покрытия и электродной проволоки, а также на промышленном производстве.
Состав и структура
Сварочные электроды состоят из трех основных элементов, каждый из которых выполняет свою функцию.
1. 1. Металлический или неметаллический стержень. Основа электрода — это холоднотянутая проволока сечением от 0,3 до 12 мм. Для изготовления стержней используется сталь трех категорий:
• Углеродистая — для сварки углеродистой и низколегированной стали;
• Легированная — для соединения деталей из легированной, конструкционной и жаропрочной стали;
• Высоколегированная — для работы с нержавеющей сталью, хромоникелевыми и хромистыми сплавами.
2. Покрытие или обмазка. Некоторые электроды имеют покрытие или обмазку, которая наносится на поверхность стержня. Оно состоит из специальных химических соединений и добавок.
✓ У некоторых марок покрытие может отсутствовать.
Покрытие выполняет несколько важных функций:
• Защита расплава сварочной ванны от кислорода;
• Металлургическая обработка сварочной ванны;
• Создание защитного газового облака во время сварки.
3. Контактный наконечник— это концевая часть, которая обеспечивает электрическую связь между электродом и сварочным аппаратом. Контактный наконечник позволяет подключить электрод к сварочному проводу или держателю.
В процессе сварки металлический стержень плавится, заполняя сварную ванну расплавленным металлом. Одновременно плавится и обмазка, которая покрывает тонким слоем расплавленный металл и создает защитное газовое облако, перекрывающее доступ кислорода к области сварки.
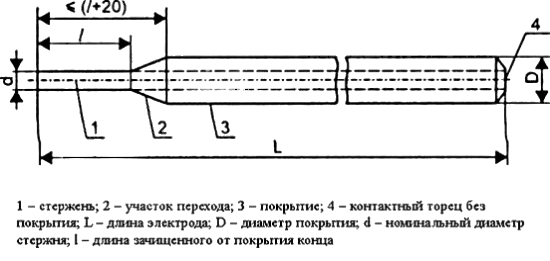
Назначение
1. Формирование сварного шва. Выбор типа электрода влияет на глубину прогрева металла, быстроту розжига и стабильность электрической дуги. Качественный шов требует правильного подбора электрода, который имеет нужные химические свойства сварного соединения.
2. Поддержание стабильной дуги. Электрод должен обеспечивать стабильность электрической дуги на протяжении всего процесса. Устойчивая дуга влияет на равномерное плавление и заполнение сварной ванны.
3. Защита расплава сварочной ванны. Покрытие (обмазка) при плавлении создаёт защитное газовое облако вокруг дуги сварки. Это облако предотвращает доступ кислорода к сварочной зоне, что предотвращает окисление и загрязнение сварочного шва.
4. Снижение разбрызгивания. Правильно подобранный электрод снижает разбрызгивание расплавленного металла во время сварки — это помогает создать более аккуратный шов.
5. Легкое удаление шлака. Электроды должны обеспечивать легкое отделение и удаление шлака с поверхности сварного соединения. Это позволит достичь чистого и шва.
6. Повышение прочности и ударной стойкости сварного соединения. Это особенно важно при сварке конструкций и деталей, где требуется высокая надежность.
Виды
Для точечной сварки
Для точечной сварки характерны сохранение первоначальной формы соединяемых деталей и обеспечение необходимой степени электропроводимости.
Оборудование для точечной сварки использует специальные контакты: стержни из медных сплавов с плоской, сферической или заостренной рабочей поверхностью.
✓ Одним из недостатков такой сварки является отсутствие герметичного шва.
Для наплавки
Для выполнения наплавки металла используются электроды, которые восстанавливают или изменяют параметры изделий, повышают износостойкость, механическую и коррозионную прочность.
Суть наплавки заключается в плавлении сердечника под воздействием сварочной дуги и нанесения нового слоя металла на обрабатываемую поверхность.
Для достижения эффективных результатов необходимо правильно подобрать электроды и строго соблюдать технологию наплавки. Материал наплавочных электродов должен тщательно соответствовать материалу, на который осуществляется наплавка, чтобы предотвратить возникновение внутренних напряжений и обеспечить качественное соединение.
ОЗН-300М, ОЗН-400М — используются для упрочнения металлообрабатывающих инструментов;
УОНИ 13/НЖ-20Х13, ЦН-6Л, ЦН-12М — применяются при обработке нержавеющей стали;
Т-590, Т-620, ОЗН-6, АНП-13 — подходят для работы с низколегированными сталями.
Плавящиеся
Эти электроды содержат сердечник, который плавится под воздействием электрической дуги. В результате плавления сердечника образуется расплавленный металл, который заполняет сварочную ванну и формирует сварной шов. Обмазка создает защитную газовую среду, которая предотвращает попадание посторонних примесей в сварочную ванну.
Качество сварного шва зависит от близости состава материала стержня и свариваемой заготовки. Чем ближе, тем выше качество и прочность сварного соединения.
Неплавящиеся
Это овальные удлиненные стержни, изготовленные из порошкообразных материалов: аморфный уголь или вольфрам. Они обеспечивают хорошее сцепление между соединяемыми деталями. В отличие от плавящихся электродов, материал стержня не плавится, а служит в качестве присадочной проволоки, которая формирует четкие сварные швы.
Часто применяются для воздушно-дуговой резки толстого металла. Обладают хорошей прочностью и стабильностью при работе с высокими температурами, что позволяет эффективно резать металлы большой толщины.
Для углеродистых и низколегированных сталей
Такие стали характеризуются низкой теплостойкостью и низким сопротивлением разрыву (не более 500 МПа). Рекомендуется использовать специальные электроды с различными типами обмазки: рутиловой, основной или смешанной.
✓ Популярные марки: АНО-4, АНО-6, МР-3, МР-3С, ОЗС-6, УОНИ 13/45 и УОНИ 13/55. У них оптимальные характеристики для создания прочных и надежных сварных соединений в этом типе сталей
Для нержавеющей стали
Для сварки нержавеющей стали, которая обладает высокой прочностью и устойчивостью к коррозии, но имеет некоторые ограничения в свариваемости, необходимо использовать специальное оборудование и расходные материалы. Выбор электродов зависит от типа и состава стали, а также от требуемых сварочных характеристик. Лучше всего подойдут с рутиловой, основной или смешанной обмазкой.
Для сварки и наплавки чугуна
Чугун, благодаря высокому содержанию углерода в его структуре, обладает рядом особенностей: высокая твердость, пористость и хрупкость, низкая ударная вязкость и пластичность. Однако, из-за присутствия крупных вкраплений графита в его структуре, чугун плохо поддается сварке и требует тщательного подбора присадочных материалов.
МНЧ-2 — стержни состоят из никеля, меди, марганца и железа и предназначены для сварки, наплавки и заварки дефектов любого типа чугунных изделий на постоянном токе обратной полярности. Образуют прочный, стойкий к коррозии, шов и не требуют предварительной прокалки. Имеют легкий поджиг, стабильное горение дуги и быстрое отделение шлаковой корки.
ОЗЧ-2 — медные электроды с кислым покрытием. Только для работы с ковким и серым чугуном. Создают прочный шов повышенной плотности и подходят для комплексной многослойной наплавки. При этом первые слои выполняются с использованием электродов МНЧ-2 или ЦЧ-4, а последующие слои выполняются с использованием стержней ОЗЧ-2.
ОЗЧ-4 — предназначены для холодной сварки и наплавки любого вида чугуна в нижнем и вертикальном положении на постоянном токе обратной полярности. Образуют прочный шов с высокой сопротивляемостью к истиранию. Требуют предварительной прокалки в течение часа при температуре 260-280 °C.
ОК 92-18 — универсальные электроды с основным покрытием, содержащим высокое содержание графита. Подходят для работы на пониженных постоянных и переменных токах и используются для заварки дефектов и повреждений корпусов насосов, коробок передач, деталей двигателей.
ЦЧ-4 — с основным покрытием. Предназначены для горячей и холодной сварки серого, ковкого и высокопрочного чугуна, наплавки и заварки дефектов. Более эффективный результат достигается, если первые один-два слоя выполняются с использованием других специальных электродов.
✓ Электроды марок МНЧ-2, ОЗЧ-4 и ОЗЧ-2 могут использоваться для холодной сварки без предварительного прогрева металла, в то время как электроды марок ОК 92.18 и ЦЧ-4 выполняют сварку горячим методом и требуют предварительной прокалки чугуна при температуре +500...+600 °C.
Для цветных металлов
Сварка цветных металлов отличается от сварки стали из-за существенных различий в показателях температуры плавления, теплопроводности и других технических характеристик. Каждый тип металла требует специализированных электродов, которые имеют подходящие сварочные характеристики и минимизируют возможные дефекты.
Алюминий
Одной из особенностей алюминия является наличие плотной и тугоплавкой оксидной пленки на поверхности, которая затрудняет формирование сварного шва. Для предотвращения образования «непроваров» рекомендуется использовать графитовые электроды МПГ-6 или стержни с обмазкой, содержащие щелочноземельные металлы, хлористые и фтористые соединения. Эти компоненты способствуют удалению оксидной пленки и стабилизируют горение дуги. Подходящие марки: ОЗАНА-1, ОЗА-1, ОК 96.10 (для чистого алюминия) и ОЗАНА-2, ОЗА-2, ОК 96.50 (для алюминиевых сплавов).
✓ Сварку следует выполнять на постоянном токе обратной полярности
Никель и сплавы
Чувствительны к примесям и склонны к трещинообразованию. Для получения качественного результата необходимо использовать электроды высокой чистоты: Н-10, НП1, Н-37 (для чистого никеля), УОНИ-13/45 (для никеля и медно-никелевых сплавов), ЦТ-28, ИМЕТ-4, ИМЕТ-7, ИМЕТ-4П (для хромоникелевых сплавов) и ОЗЛ-17У (для железоникелевых сплавов).
Медь и сплавы
Медь обладает высокой электро- и теплопроводностью, повышенной текучестью расплава и активным взаимодействием с кислородом и водородом, что может привести к образованию трещин в процессе сварки. Чтобы избежать таких проблем нужно тщательно очистить свариваемые элементы и провести прокаливание электродов. Подходящие марки: Комсомолец-100, ОМЗ-2, ОМЗ-3, ОМЗ-4.
Сварка на постоянном токе
Применяется для тонкостенных изделий. На таком токе электрод подключается к положительному выводу сварочного источника, а деталь - к отрицательному.
ЦЛ-11. Диаметр стержня составляет 3 мм. В состав входят хром, никель и молибден. Рекомендуются для изделий, эксплуатируемых в агрессивной среде при температуре до 450 °C.
НЖ-13. Высокий коэффициент наплавки. Рекомендуются для емкостей из хромоникелемолибденовой пищевой стали, которые предназначены для транспортировки и хранения пищевых продуктов в условиях повышенных температур.
НИИ-48Г. Для соединения высокомарганцовистых и аустенитных хромоникелевых жаростойких сталей, которые эксплуатируются в агрессивной среде.
✓ При выборе важно обратить внимание на рекомендуемые значения силы тока, указываемые на упаковке
Сварка на переменном токе
ЛЭЗ-8 — комбинированные стержни с рутиловой обмазкой, которые подходят для конструкций из хромоникелевых сплавов как при переменном, так и при постоянном сварочном токе.
ОЗЛ-14 — для нержавеющих хромоникелевых сплавов без особых требований к качеству металла шва.
ОЗЛ-14А — с рутиловой обмазкой для сварки на постоянном токе обратной полярности, однако можно использовать и при переменном токе. Они формируют шов, обладающий устойчивостью к межкристаллитной коррозии и повышенной стойкостью к высоким температурам до 650 °C.
ЦТ-50 — рутиловые, с металлическим стержнем, содержащие около 22% хрома и до 10% никеля. Для высоколегированной нержавеющей стали при переменном или постоянном токе. Повышенная устойчивость к фтористым соединениям и кислотам.
Н-48 — с основным покрытием, которые рекомендуются для конструкций, эксплуатируемых в неокислительных агрессивных средах при температуре не выше 300 °C.
АНВ-36 — тоже с основным покрытием. Применяются для металла, эксплуатируемого при температуре до 500 °C.
✓ Для сварки изделий из нержавеющей стали чаще применяется постоянный ток
Про покрытие
Обмазка сварочного электрода представляет собой гомогенизированную массу из различных химических компонентов. Ее задача — создать непрерывное горение и придать сварному соединению определенные свойства. В зависимости от состава обмазки выделяются различные разновидности.
Одним из видов обмазки является кислое покрытие, обозначаемое буквой "А". Состоит из оксидов марганца, железа и кремния. Применяется для сварки низкоуглеродистых сталей, особенно в горизонтальном положении.
+ Преимущества: стабильная дуга, хорошо работает на поверхности с ржавчиной
— Недостатки: токсичность, высокая текучесть металла шва, недостаточная чистота и повышенная концентрация водорода в сварочной ванне
Другой вид обмазки — основное покрытие, обозначаемое буквой "Б". Состоит из фтористых соединений и карбонатов. Стержни с основным покрытием применяются для сварки толстых заготовок и конструкций, работающих при высоких нагрузках.
+ Преимущества: прочные, чистые и устойчивые к трещинообразованию швы с высокой пластичностью и ударной вязкостью
— Недостатки: образование короткой нестабильной дуги, трудности с отделением окалины, проблемы при хранении
✓ При сварке особо важных конструкций с использованием инвертора рекомендуется выбирать стержни с основным покрытием. Они обеспечивают более стабильную сварочную дугу и качественный шов.
Ещё один вид — рутиловое покрытие, обозначаемое буквой "Р". Состоит из минерала рутил, ферромарганца, кремнезема, карбоната кальция или магния. Такие стержни подходят для строительных конструкций и изделий из низколегированных сталей в любых положениях.
+ Преимущества: высокое качество шва, легкое отделение шлака, минимальное разбрызгивание металла
— Недостатки: сильная текучесть, низкая химическая чистота шва, повышенная концентрация водорода в сварочной ванне
✓ Для изделий из углеродистой стали с увлажненной или ржавой поверхностью рекомендуется использовать рутиловые электроды. Они обладают хорошей восстановительной способностью и могут эффективно работать с такими поверхностями. Например AG E-46 PREMIUM отлично справятся с такой задачей
Также есть целлюлозное покрытие, обозначаемое буквой "Ц". Содержат в обмазке натуральную целлюлозу, ферросплавы и органические смолы.
+ Преимущества: хороший провар на постоянном токе, использование в любом пространственном положении, небольшое количество плотного и вязкого шлака
— Недостатки: высокая концентрация водорода, понижающая пластичность сварного шва, большой расход из-за разбрызгивания металла
Существуют и смешанные типы покрытий: рутилово-целлюлозные (РЦ), рутилово-основные (РБ), кисло-рутиловые (АР), рутиловые с железным порошком (РЖ) и другие. Комбинация компонентов обмазки позволяет достичь стойкости к вибрациям, перепадам температур и силовым нагрузкам.
Разнообразие типов обмазки обусловлено требованиями к сварке различных материалов и условиям эксплуатации сварных соединений. Выбор определенного типа электрода зависит от сварочных характеристик, требований к прочности и качеству шва, а также специфических условий работы.
Покрытия | Обозначения ГОСТ | Обозначения ISO (международное) |
Кислые | А | A |
Основные | Б | B |
Рутиловые | Р | R |
Целлюлозные | Ц | C |
Кисло-рутиловые | АР | AR |
Рутилово-основные | РБ | RB |
Рутилово-целлюлозные | РЦ | RC |
Рутиловые с железным порошком | РЖ | RR |
Прочие | П | S |
Про диаметр, длину, вес и производительность
Один из основных параметров — диаметр стержня. Выбор зависит от толщины свариваемого металла и сварочного оборудования. Чем толще металл, тем больше должен быть диаметр. Это создаст достаточную мощность для прогрева и плавления металла, а также стабильную дугу.
Длина электрода имеет значение в ситуациях, когда нежелательны перерывы в процессе сварки. Например, при ремонте трубопроводов под давлением. Есть различные размеры, обычно от 150 до 450 мм. Более длинные помогут сварщику выполнять работу без необходимости частого перезапуска сварки.
Вес тоже важен. Легкие электроды удобнее для работы в технически сложных позициях, а у тяжелых лучше стабильность дуги и выше скорость сварки.
Помимо размеров есть характеристики, которые влияют на сварочные свойства и производительность: положительная полярность (ПП) или отрицательная полярность (ОП), ток нагрева (Ампер), выход металла (кг/ч).
Диаметр стержня, мм | Сварочный ток, Ампер | Толщина заготовки, мм |
1.6 | 25-50 | 1-2 |
2 | 40-80 | 2-3 |
2.5 | 60-100 | 2-3 |
3 | 80-160 | 3-4 |
4 | 120-200 | 4-6 |
5 | 180-250 | 6-8 |
6 | 220-320 | 10-24 |
6-8 | 300-400 | 30-60 |
Классификация по ГОСТ
Производство металлических электродов для ручной дуговой сварки и наплавки сталей регламентируется ГОСТ 9466-75. В соответствии с этим стандартом сварочные электроды подразделяются на различные группы и классы в зависимости от параметров. Классификация по ГОСТ помогает определить назначение, вид тока, толщину покрытия и пространственное расположение наплава.
Классификация по назначению
"У" — для соединения углеродистых и низкоуглеродистых материалов с сопротивлением на разрыв до 600 МПа;
"Л" — для конструкционных и легированных сталей с сопротивлением на разрыв до 600 МПа;
"Т" — для термостойкой легированной стали;
"В" — для высоколегированных материалов с особыми свойствами;
"Н" — для наплавки.
Классификация по виду тока
Сварка производится на постоянном или переменном токе.
Постоянный ток обеспечивает лучший шов, высокую производительность и низкий уровень разбрызгивания. Однако требует дорогостоящего оборудования.
Переменный ток доступнее с точки зрения стоимости трансформаторов, но имеет меньшую стабильность дуги и больший расход материалов.
Толстые металлы свариваются на постоянном токе прямой полярности, в то время как для работы с тонкими металлическими листами применяют ток обратной полярности, чтобы предотвратить прожигание материала.
Классификация по толщине покрытия
"М" — с тонким покрытием;
"С" — со средней толщиной покрытия;
"Д" — с толстым покрытием;
"Г" — с особо толстым покрытием.
✓ Толщина покрытия определяется соотношением диаметра электрода (D) к диаметру стержня (d).
Классификация по пространственному расположению наплава
"1" — сварка возможна в любом положении;
"2" — в любом положении, за исключением сверху-вниз;
"3" — работа в вертикальном положении, включая сверху-вниз, а также горизонтальное и нижнее положение;
"4" — в нижнем положении.
Пример маркировки сварочных электродов
Маркировка сварочных электродов, состоящая из буквенных и цифровых символов, является важным элементом их идентификации и предоставляет информацию о характеристиках и свойствах. Ниже приведены примеры маркировки электродов и их расшифровка:
Маркировка УОНИ-13/55:
У: Универсальный электрод
О: Обмазка
НИ: Научно-исследовательский институт
13: Номер института
55: Прочность на разрыв, выраженная в кгс/мм²
Маркировка Э46-МП-3:
Э: Электрод сварочный
46: Удельное сопротивление разрыву
МП-3: Марка электрода
Эти данные позволяют определить производителя, прочностные характеристики и другие параметры. Маркировка может варьироваться в зависимости от стандартов и производителей. Следует обращаться к технической документации.
Правила хранения
В соответствии с ГОСТом соблюдение условий хранения сварочных электродов является важным фактором для их долговечности и обеспечения высокого качества сварочных работ.
✓ Температура хранения. Электроды должны храниться при температуре не ниже 15 °C. Низкие температуры вызывают осыпание обмазки и ухудшат прожигание, что приводит к получению некачественных сварочных швов.
✓ Влажность в помещении не должна превышать 50%. Высокий показатель приведёт к залипанию стержней.
✓ Защита от загрязнений. Электроды должны быть защищены от пыли и грязи. При загрязнении качество сварки ухудшится.
✓ Избегать механических повреждений. Удары, падения и другие воздействия приведут к трещинам или обломкам на стержнях, что снизит их качество.
Рекомендуется хранить электроды в защитные упаковки или контейнерах
Сушка и прокалка
Сушка и прокалка имеют важное значение для обеспечения оптимальных сварочных характеристик.
✓ Прокалка — процедура нагревания для удаления влаги из обмазки. Продолжительность и температура указываются в инструкции, прилагаемой к каждой заводской упаковке. Важно следовать указаниям производителя и не превышать рекомендованные параметры, чтобы избежать негативного влияния на свойства электродов.
✓ Оптимальное количество прокалок. Не рекомендуется проводить прокалку заранее, поскольку неиспользованные материалы все равно потребуется прокалить повторно перед использованием. Прокалка может быть выполнена не более трех раз. Последующие негативно повлияют на свойства электродов.
✓ Влияние влаги на сварочный процесс. Влага, содержащаяся в стержнях, вызовет плохое прожигание, неравномерное горение дуги и некачественное формирование сварного шва. Необходимо убедиться, что электроды хранятся и транспортируются в сухих условиях до момента их использования.
Сушка и прокалка должны проводиться согласно рекомендациям производителя. Это поможет гарантировать оптимальные сварочные характеристики и качество сварки.
Советы
Чем руководствоваться при выборе:
✓ Соответствие состава электрода и свариваемого материала.
✓ Диаметр электрода.
С его увеличением плотность сварочного тока снижается. Это может привести к неустойчивой сварочной дуге, увеличению ширины сварного шва и ухудшению провара деталей. Подберите диаметр электрода в соответствии с требованиями и рекомендациями для вашей задачи.
✓ При выборе значения силы тока руководствуйтесь рекомендациями, указанными на упаковке электродов.
Ещё несколько факторов, на которые стоит обратить внимание:
✓ Убедитесь, что электроды были изготовлены недавно. Хранение в соответствии с рекомендациями производителя играет важную роль в сроке годности. Если неизвестно, были ли условия хранения соблюдены, выбирайте продукцию, которая изготовлена не более 6 месяцев назад.
✓ Обратите внимание на толщину обмазки. Она должна быть равномерной и одинаковой со всех сторон. Покрытие не должно иметь сколов или повреждений. Осмотрите концы стержней - они не должны иметь признаков ржавчины, белого налета или осыпания обмазки.
✓ Упаковка не должна содержать следов влаги.
Если вы не уверены в качестве электродов, лучше отказаться от их покупки, чтобы избежать потенциальных рисков и проблем.
Безопасность
При выполнении сварочных работ очень важно обеспечить свою безопасность. Необходима защитная одежда:
1. Маска или щиток защитят лицо и глаза от вредных воздействий света и брызг металла. Рекомендуется использовать маску с автоматическим затемнением — маску-хамелеон. Она автоматически темнеет при поджоге дуги, обеспечивая необходимую защиту, и снова становится светлой после окончания работы.
2. Перчатки или краги для защиты рук от тепла, искр, брызг металла.
3. Куртка, штаны и закрытая обувь. Все части тела должны быть полностью закрыты, чтобы предотвратить попадание брызг металла или искр на кожу.
Все части тела должны быть полностью закрыты, чтобы предотвратить попадание брызг металла или искр на кожу. Не забывайте, что защитная амуниция является неотъемлемой частью и ее использование должно быть обязательным при выполнении сварочных работ.
В нашем интернет-магазине вы найдете широкий выбор электродов, подходящих для различных материалов и задач. Покупая у нас, вы получаете качественные и надежные продукты для эффективной сварки. Оформите заказ сегодня и уже на следующий день вы получите нужные позиции. Если у вас возникли вопросы или требуется дополнительная консультация — свяжитесь с нашей командой! Мы всегда готовы помочь вам с выбором и предоставить профессиональную поддержку.
|
Нужна консультация
|